How do metallic finishes on droppers influence luxury branding?
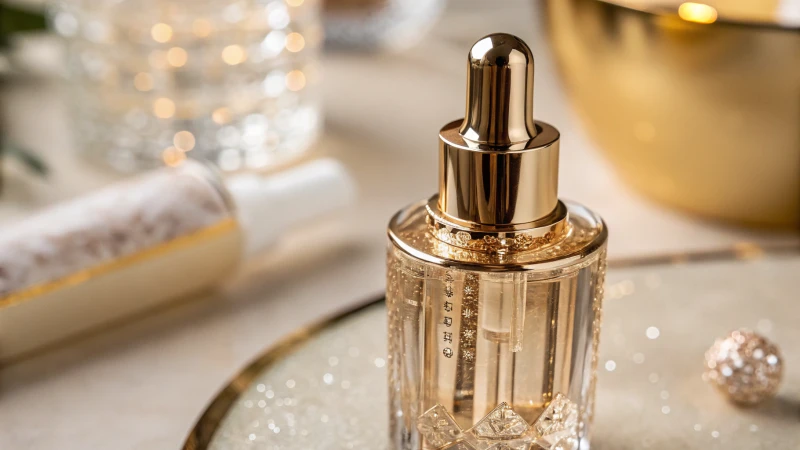
Metallic finishes on droppers play a crucial role in luxury branding by conveying quality, exclusivity, and sophistication. They enhance product appeal and differentiate brands in a competitive market. However, these finishes introduce complexities in production processes and sustainability challenges. As consumer demand for eco-friendly products rises, brands must balance aesthetics with responsible practices. Collaborating with innovative suppliers can help navigate these challenges while maintaining high-quality standards. Ultimately, metallic finishes not only elevate visual allure but also tell a brand’s story, making them an essential element of modern luxury packaging.
What are the pros and cons of screen printing vs. hot stamping on cosmetic glass bottles?
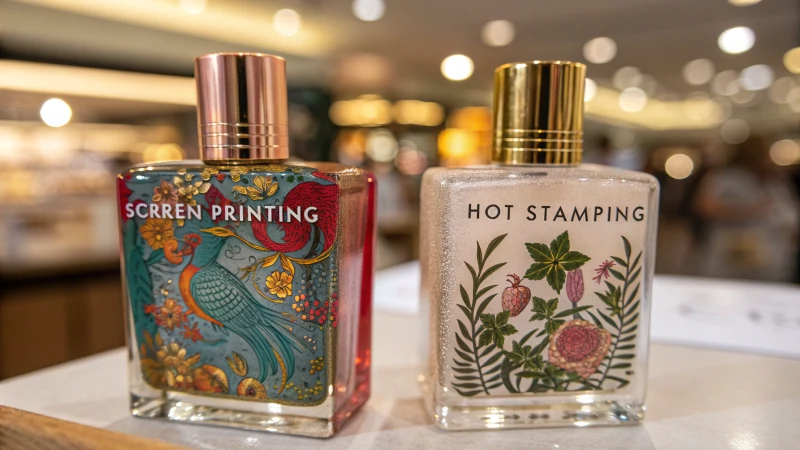
This article explores the pros and cons of screen printing versus hot stamping for cosmetic glass bottles. Screen printing is known for its durability, vibrant colors, and cost-effectiveness in large runs, making it suitable for intricate designs. In contrast, hot stamping delivers a luxurious metallic finish that enhances brand appeal but comes at a higher cost per unit. The choice between these methods depends on factors such as production volume, design complexity, and desired aesthetic. Understanding these differences can help brands make informed decisions to elevate their packaging strategy.
How to achieve long-lasting labeling on cosmetic glass surfaces?
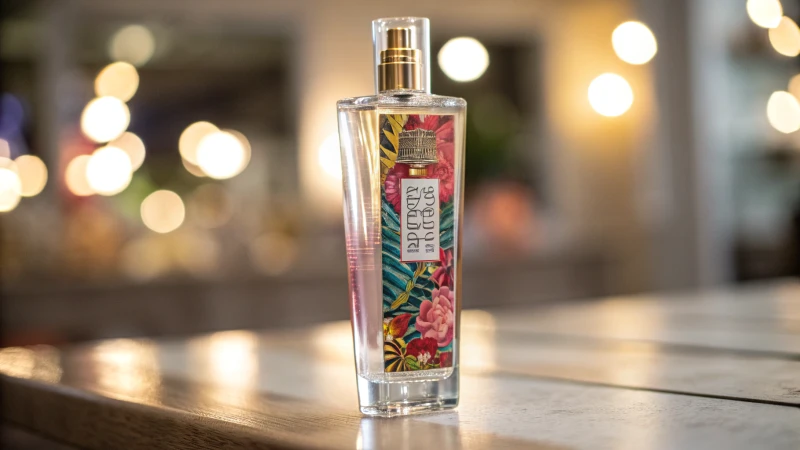
Achieving long-lasting labels on cosmetic glass involves selecting the right adhesive, treating surfaces effectively, and using durable printing methods. Techniques such as sandblasting and UV printing enhance adhesion and resistance to environmental factors. Eco-friendly options are increasingly important in today’s market. By understanding the properties of materials and employing protective coatings, brands can ensure their packaging remains visually appealing while withstanding moisture, temperature fluctuations, and UV exposure. This guide explores various strategies to improve label longevity, including advanced technologies like laser micro-processing and nano-coating. Ultimately, prioritizing quality in labeling will enhance customer experience and reduce long-term costs.
What inspection tools are used for checking glass bottle dimensions?
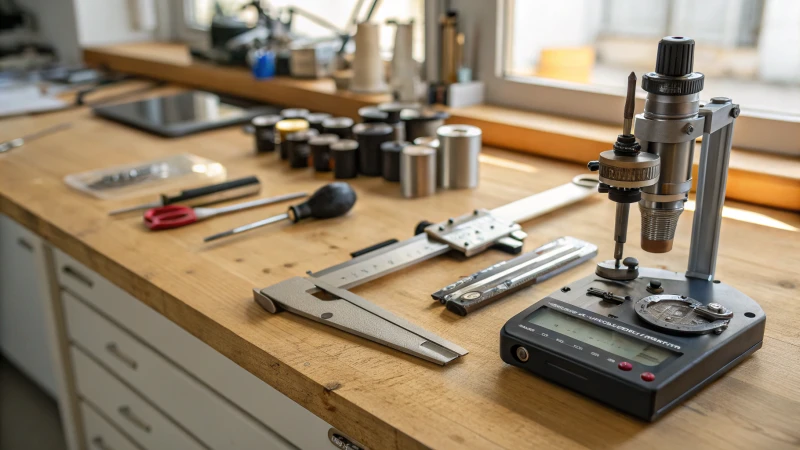
This article explores the various inspection tools used to measure glass bottle dimensions accurately. It highlights the importance of tools like vernier calipers, micrometers, coordinate measuring machines (CMM), laser scanning systems, and optical measurement technologies. Each tool offers unique advantages in terms of precision and speed, essential for maintaining quality standards in glass bottle manufacturing. The impact of temperature on glass dimensions is also discussed, emphasizing how thermal expansion can affect product fit and stability. Additionally, the article addresses challenges in achieving consistent wall thickness and the significance of international standardization for compatibility across global markets. By understanding these factors and employing advanced measurement techniques, manufacturers can enhance operational efficiencies while ensuring customer satisfaction.
How to perform a drop test on glass bottles to check durability?
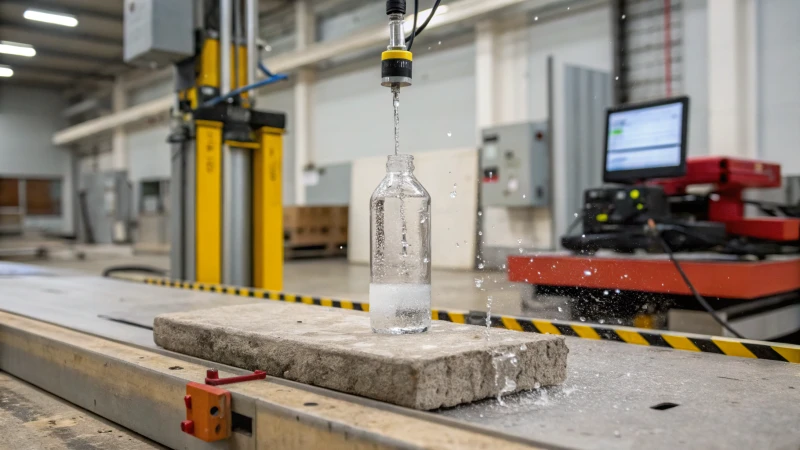
This guide details the process of performing a drop test on glass bottles to evaluate their durability. It covers essential equipment, safety precautions, and testing methods, including varying drop heights and orientations. By understanding how material type and bottle shape influence results, manufacturers can enhance packaging design for better resilience against impacts. The article emphasizes the importance of systematic testing in real-world scenarios to ensure product safety and integrity during transport. Key insights include the significance of using appropriate materials like borosilicate glass and optimizing designs for maximum impact absorption. Conducting thorough drop tests helps prevent breakage and leakage, ultimately improving customer satisfaction with durable packaging solutions.
What is the best way to add gradient colors to glass drop bottles?
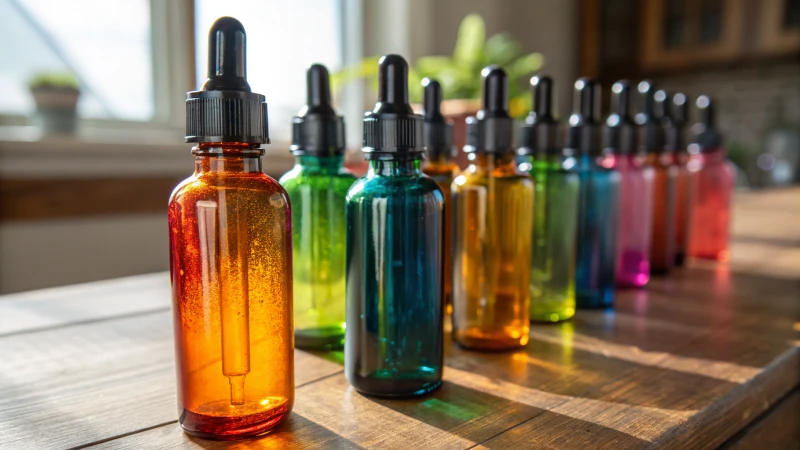
This blog post delves into the best methods for adding gradient colors to glass dropper bottles. Techniques such as screen printing with gradient inks, airbrushed frosting, dip dyeing, heat transfer printing, and two-tone spraying are explored. Each method offers unique advantages in terms of precision, durability, and cost-effectiveness. The importance of selecting the right glass material—like low-iron glass for enhanced clarity—and understanding light interaction is emphasized. Additionally, practical considerations for designers regarding quality control and regional market preferences are discussed to ensure successful implementation of gradient designs that resonate with consumers.
What are the most popular printing methods for branding glass drop bottles?
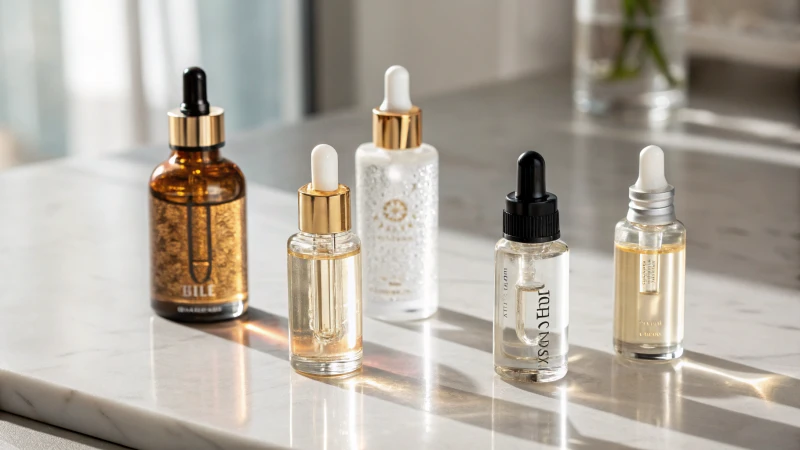
This article delves into the most popular printing methods for branding glass dropper bottles. It covers techniques such as silkscreen printing, known for its cost-effectiveness and durability; hot stamping, which provides a luxurious metallic finish; pad printing for intricate designs on curved surfaces; UV printing that enhances color vibrancy; laser engraving for permanent marks; and decal printing suitable for complex designs. Each method has distinct benefits tailored to different branding requirements and product styles. Understanding these options can help brands choose the right technique to effectively convey their identity and appeal to consumers.
What are the energy-saving technologies in cosmetic glass bottle production?
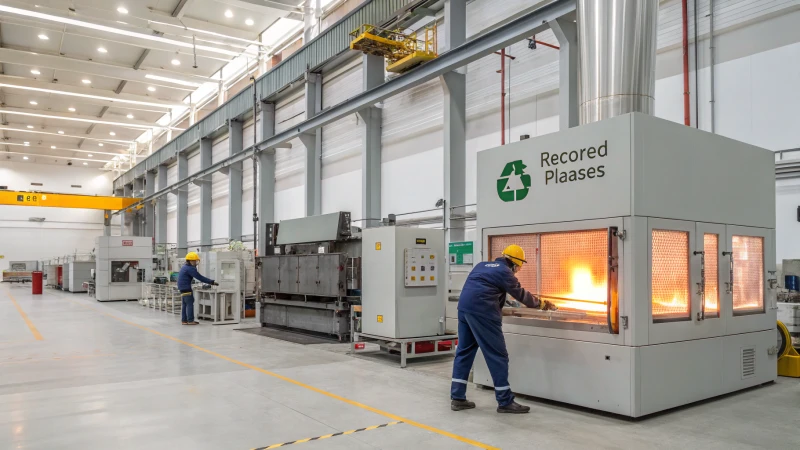
The cosmetic glass bottle production industry is embracing energy-saving technologies to enhance sustainability and reduce costs. Innovations such as electric melting furnaces and heat recovery systems significantly lower energy consumption—by up to 30%—while improving efficiency. Advanced insulation materials and the use of recycled glass further contribute to these savings, making production processes more eco-friendly. As manufacturers adopt automation and smart technologies, they not only cut costs but also align with global sustainability goals. This shift towards greener practices is essential for meeting consumer demand for environmentally responsible packaging solutions.
How to integrate logo embossing into glass drop bottle mold designs?
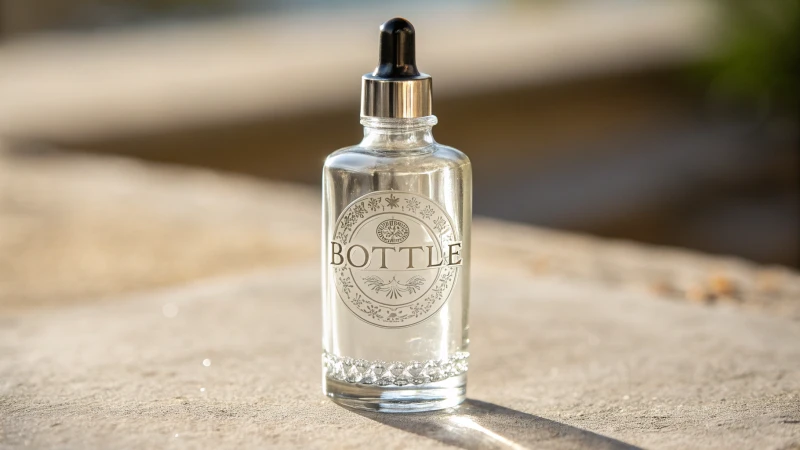
Integrating logo embossing into glass dropper bottle mold designs is essential for enhancing brand identity without compromising functionality. This process involves incorporating the logo directly into the mold, selecting durable materials like hardened steel or aluminum, and strategically placing the logo to maximize visibility while maintaining aesthetic appeal. Careful attention must be paid to potential impacts on glass thickness and weight distribution to ensure product stability and functionality. Regular quality control checks are crucial for consistency across production runs. Although initial costs may be higher due to specialized molds, the long-term benefits of improved brand recognition and perceived value can lead to better ROI. Future trends in embossing techniques include advanced laser technology for intricate designs and eco-friendly materials that align with sustainability goals.
How does the design of glass droppers affect precise dispensing?
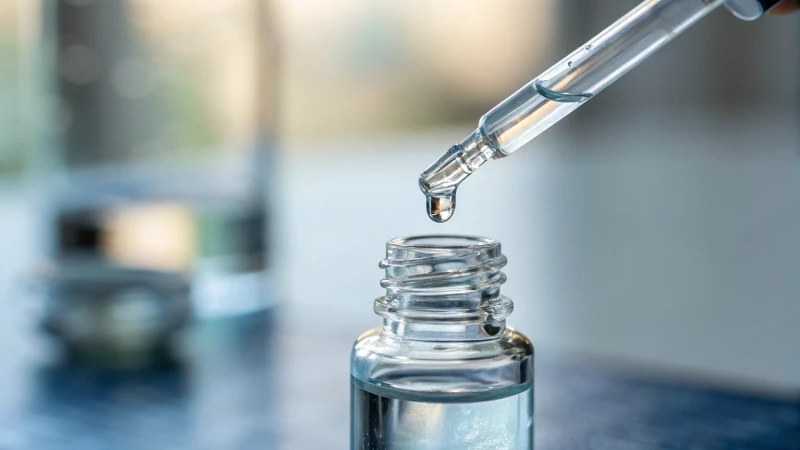
The effectiveness of glass droppers in precise liquid dispensing hinges on their design. Key elements such as the shape of the dropper tip, internal mechanisms for volume control, and the quality of materials used play critical roles in ensuring accurate dispensing. A sharp or narrow tip allows for smaller droplets essential for serums, while wider tips cater to thicker liquids. Additionally, high-quality materials prevent leaks and enhance durability. Understanding these design intricacies can lead to better product outcomes and customer satisfaction in various applications from skincare to industrial uses.