What are the best practices for testing glass cosmetic packaging for impact resistance?
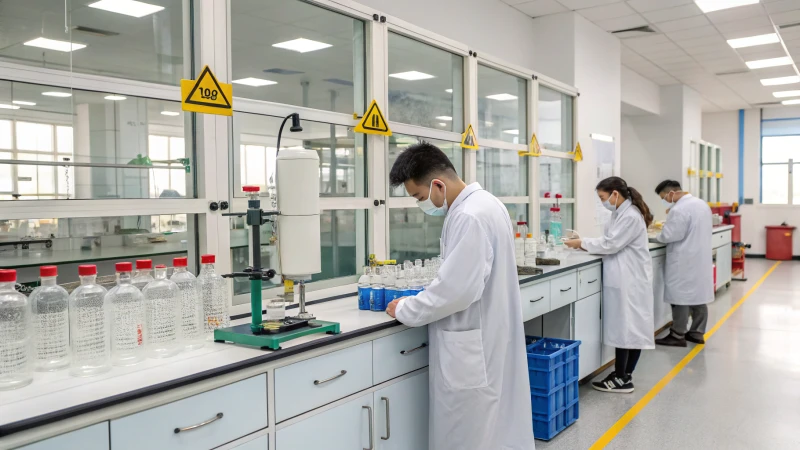
Testing glass cosmetic packaging for impact resistance is crucial to ensure durability and safety. Best practices involve conducting drop tests, pendulum impact tests, and compression strength assessments. These methods simulate real-world conditions, helping identify weaknesses in the design. Advanced techniques like AI algorithms enhance traditional testing by predicting performance based on material composition and structural design. Understanding the molecular structure of glass also plays a vital role in improving impact resistance. Innovations such as ion exchange, thermal tempering, and nano-coatings further strengthen glass products against impacts while maintaining aesthetic appeal. Real-world simulations provide insights into how products will perform under actual usage scenarios, ensuring they meet consumer expectations and industry standards.
How do I ensure my glass containers are leak-proof during transportation and handling?
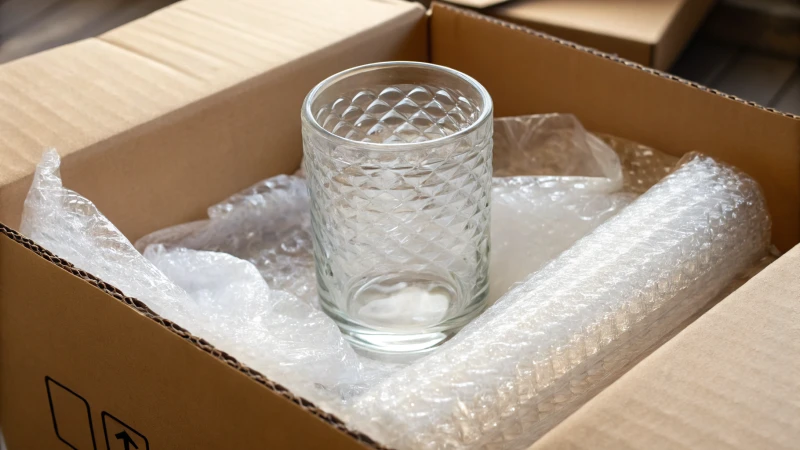
Transporting glass containers without leaks requires careful preparation. Individually wrapping each container with bubble wrap, using high-quality sealing materials like silicone or aluminum foil liners, and conducting rigorous testing such as negative pressure and vibration assessments are essential steps. Understanding the physical and chemical properties of the contents also plays a vital role in selecting appropriate liners to prevent leakage. Additionally, ensuring precise mold design can significantly enhance seal integrity. By following these best practices, businesses can ensure their products arrive intact and maintain customer satisfaction.
How do I test the compatibility of glass containers with different cosmetic formulations (e.g., fragrances, creams)?
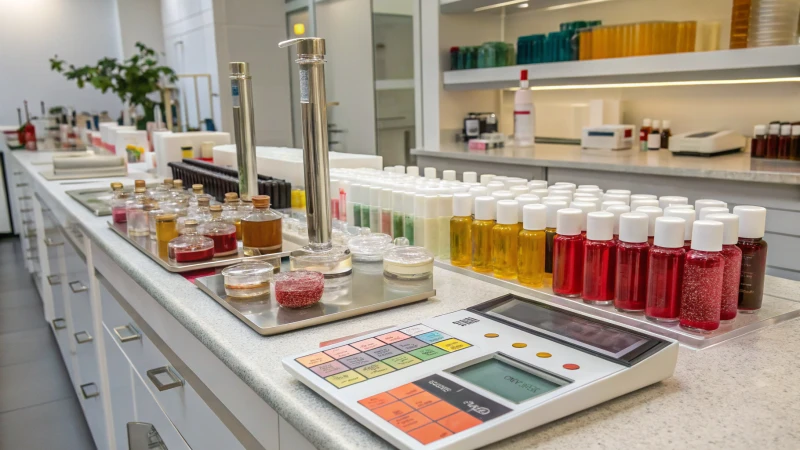
Ensuring the compatibility of glass containers with cosmetic formulations is essential for maintaining product quality. This involves selecting appropriate glass types like borosilicate for sensitive products, conducting stability tests to monitor pH and color changes, and evaluating closure systems for airtightness. Chemical interaction analysis helps detect any leaching or adverse reactions that could compromise product safety. By understanding different glass types—Type I for serums, Type II for creams, and Type III for stable products—brands can prevent costly errors and enhance customer satisfaction. Regulatory compliance with standards such as ISO 10993 ensures safety while meticulous documentation aids in traceability across international markets. This comprehensive approach not only protects the integrity of cosmetics but also builds consumer trust in brand offerings.
What are the cost differences between recyclable glass and traditional glass for cosmetic packaging?
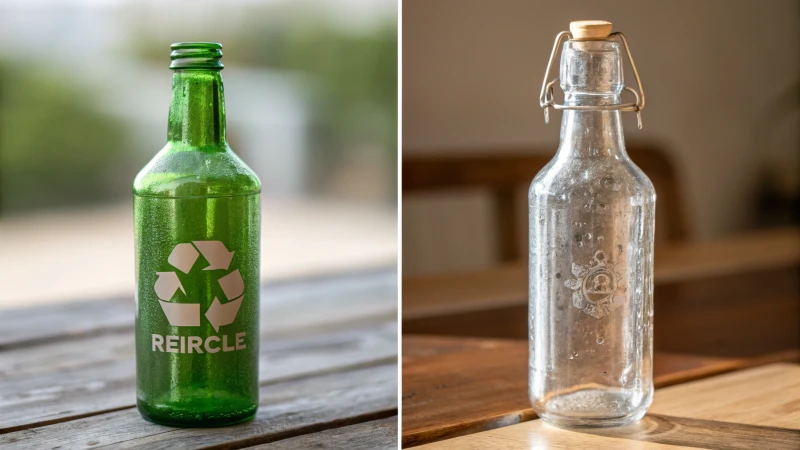
This blog post explores the cost differences between recyclable glass and traditional glass for cosmetic packaging. It highlights how factors such as raw material sourcing, energy prices, and environmental regulations contribute to the higher costs of recyclable options like Post-Consumer Recycled (PCR) glass. While PCR glass can enhance brand image and consumer loyalty through sustainability efforts, it also presents challenges in terms of production costs and supply chain complexities. The article provides insights into navigating these challenges effectively while aligning with future trends in eco-friendly packaging.
How is glass polishing done to ensure smooth, high-quality finishes on cosmetic containers?
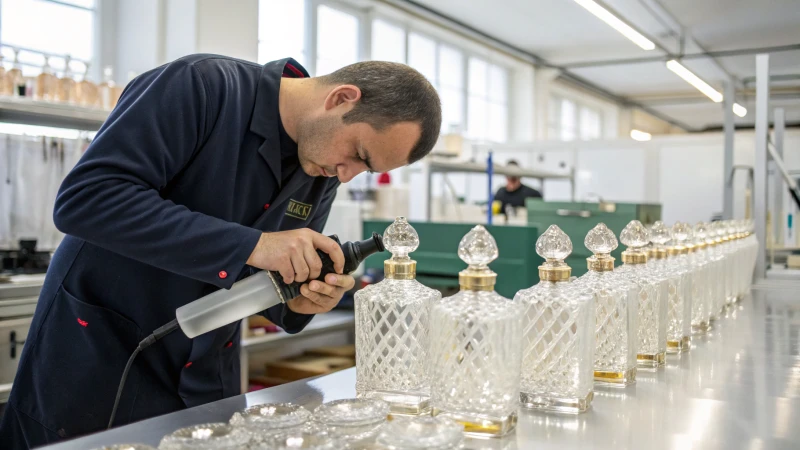
The process of glass polishing for cosmetic containers is intricate and vital for achieving high-quality finishes. It includes mechanical grinding to remove imperfections, followed by chemical polishing to enhance surface quality. The final touch is flame polishing, which creates a smooth, reflective surface that meets the luxurious standards of high-end brands. Each step ensures that the glass not only looks beautiful but also maintains durability and functionality. Understanding these processes helps manufacturers produce premium products that stand out in the competitive cosmetics market.
How does blow molding compare to press molding for creating cosmetic glass containers?
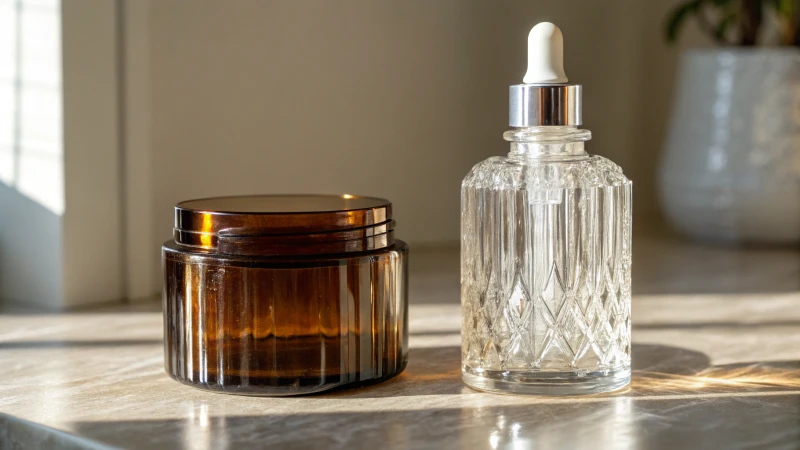
In the world of cosmetic glass packaging, blow molding offers a fast and economical solution for creating lightweight and intricately shaped bottles, making it ideal for mass-market products. In contrast, press molding is preferred for high-end applications due to its ability to produce thick-walled jars that convey luxury and quality. Each method has distinct advantages: blow molding is efficient and cost-effective, while press molding emphasizes precision and durability. Brands must consider their product design requirements, market positioning, and sustainability goals when choosing between these two methods to align with their overall strategy.
What are the costs associated with creating a custom glass mold for perfume bottles?
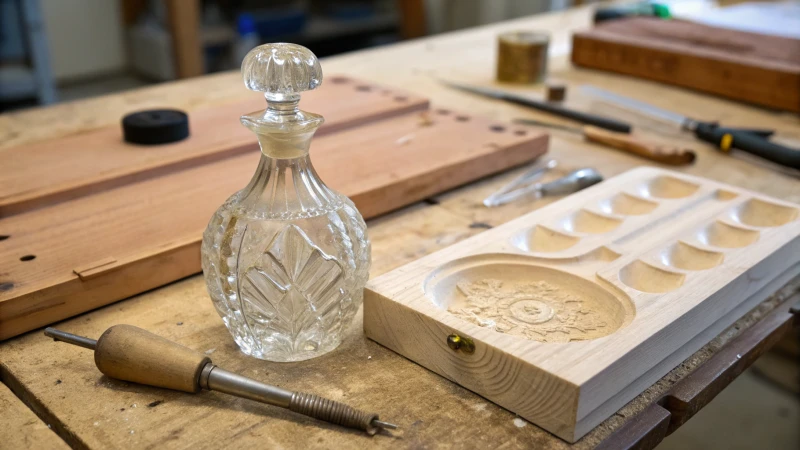
Crafting a custom glass mold for perfume bottles can be an exciting yet costly venture. Initial costs range from $5,000 to $50,000 depending on the complexity of the design and quality of materials used. Factors such as single-cavity versus multi-cavity configurations significantly impact production efficiency and per-unit costs. Additionally, hidden expenses like maintenance and testing can accumulate over time. Understanding the nuances of steel selection—between affordable Chinese options and higher-quality European alternatives—can also affect long-term durability and performance. To maximize return on investment (ROI), it’s crucial to calculate all associated costs accurately while forecasting production volume based on market demand. This comprehensive approach ensures that your investment in custom molds pays off effectively in the competitive cosmetic packaging industry.
What are the best materials for producing eco-friendly glass cosmetic packaging?
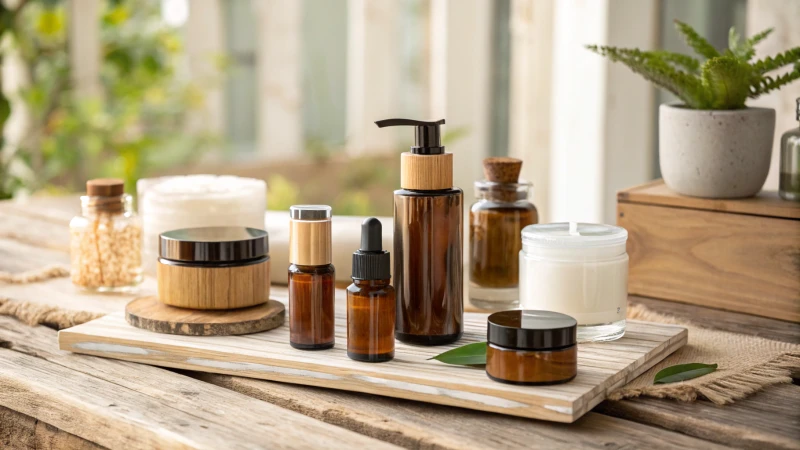
This blog post explores the best materials for eco-friendly glass cosmetic packaging, highlighting innovations such as ultra-lightweight glass, optimized mold designs, region-specific recycled blends, and low-emission furnace technology. These advancements not only minimize environmental impact but also align with consumer expectations for sustainable products. The article emphasizes the importance of closed-loop recycling systems and supply chain transparency in enhancing brand image and meeting regulatory standards. By adopting these practices, brands can significantly reduce their carbon footprints while maintaining product quality and efficiency in a competitive market.
How long does it typically take to develop a custom mold for glass cosmetic packaging?
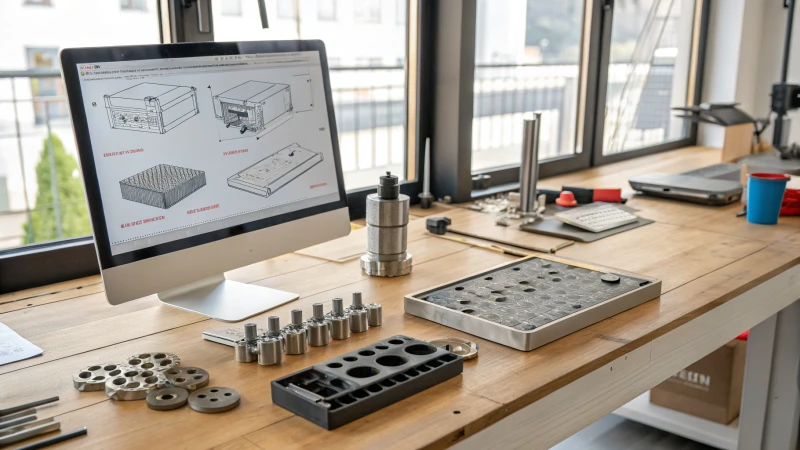
Creating custom molds for glass cosmetic packaging is an intricate process that usually spans 8 to 12 weeks. This timeline varies based on factors such as design complexity, the type of mold chosen (single-cavity or multi-cavity), and the number of necessary debugging sessions. The development process involves three key stages: design confirmation (1-2 weeks), mold fabrication (4-6 weeks), and testing adjustments (2-4 weeks). Understanding these stages and their impact on production can help streamline costs and timelines. Additionally, using pre-existing molds can significantly reduce lead times while maintaining quality. By balancing speed with cost considerations, businesses can optimize their manufacturing processes effectively.