How do I choose between clear, frosted, or colored glass for my product packaging?
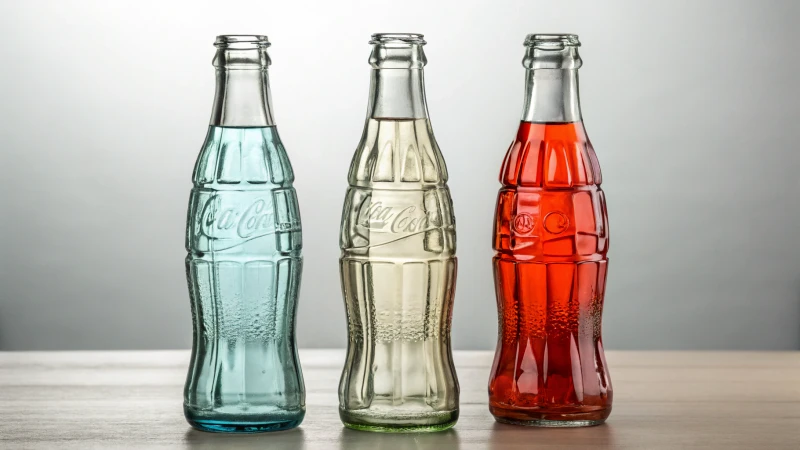
Selecting the right glass packaging—clear, frosted, or colored—requires careful consideration of your product’s protection needs, brand image, and budget. Clear glass enhances visibility but offers minimal UV protection. Frosted glass adds elegance while providing moderate light shielding. Colored glass is ideal for sensitive products needing strong UV protection. Understanding these differences can help align your packaging choice with market demands and consumer preferences while maintaining cost-effectiveness. This guide explores the advantages of each type of glass to assist in making an informed decision that balances functionality with aesthetic appeal.
What types of molds are most suitable for producing glass perfume bottles and cosmetic jars?

Selecting the right mold is crucial in producing high-quality glass perfume bottles and cosmetic jars. This article delves into four primary molding techniques: injection molds for intricate designs, blow molds for mass production of uniform jars, press and blow molds for versatility in design, and compression molds ideal for bespoke luxury packaging. Each method has its own strengths—ranging from precision to cost-effectiveness—making them suitable for different production needs. Understanding these options can help manufacturers optimize their processes and enhance product quality while meeting market demands.
What are the limitations of custom molding for glass cosmetic containers?
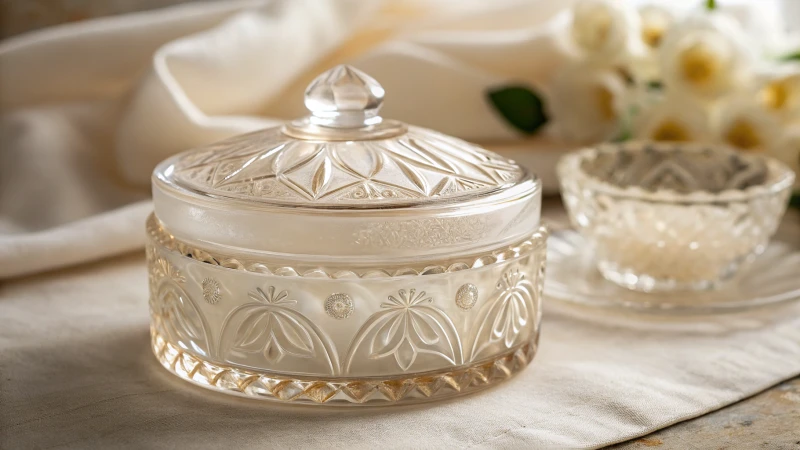
Custom molding for glass cosmetic containers offers unique design opportunities but comes with significant challenges. High initial costs, mold wear and tear, and stringent safety compliance can hinder production efficiency. To navigate these hurdles, businesses must implement effective mold lifecycle management strategies and precise temperature control during manufacturing. By focusing on proactive maintenance and leveraging advanced technologies, companies can reduce operational costs while maintaining product quality. This blog explores the limitations of custom molding in detail and provides insights into overcoming these obstacles to achieve success in the competitive cosmetic packaging market.
How do you ensure the glass containers maintain uniform quality and precision during mass production?
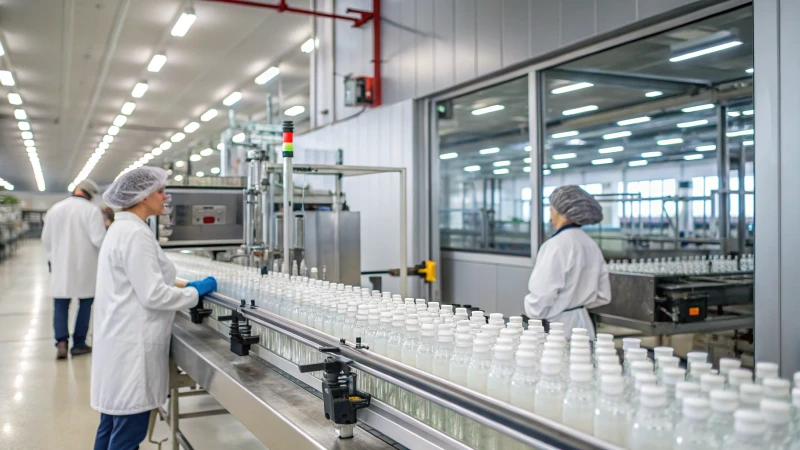
Ensuring consistent quality in glass container production involves sourcing high-quality raw materials, utilizing advanced mold design with CAD systems, implementing automated processes to reduce human error, and conducting thorough inspections. Each step is crucial for achieving uniformity and durability in the final product. Quality control measures include verifying raw material purity, precision in mold design, automated checks during production, and thermal stress testing to prevent defects. By focusing on these aspects, manufacturers can produce reliable glass containers suitable for sensitive products like cosmetics while maintaining competitive pricing.
How do I ensure my custom glass packaging is compatible with pumps, sprays, and droppers?
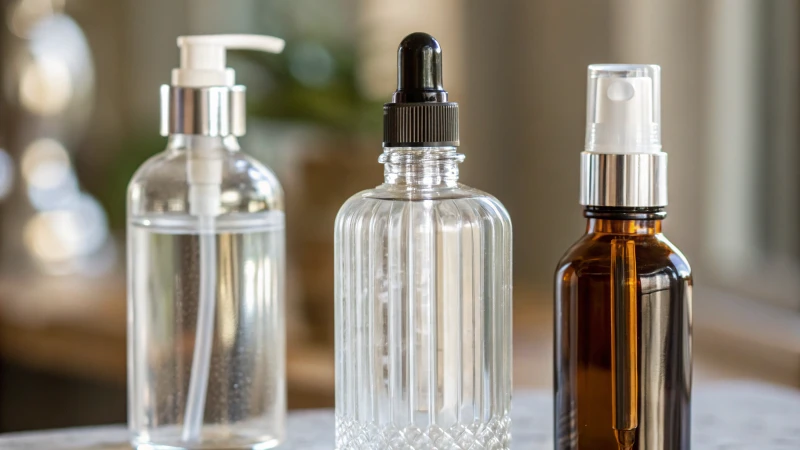
To guarantee that your custom glass packaging works seamlessly with pumps, sprays, and droppers, prioritize standardized neck sizes and threading compatibility. Collaborate closely with suppliers to conduct mock-up tests that identify potential issues like leakage or damage early in the process. Understanding material interactions is crucial; for instance, glass can crack under pressure if not paired correctly with closures. Additionally, consider airless pump designs for skincare products while ensuring they fit glass bottles without compromising integrity. Rigorous testing before mass production is essential to meet regulatory standards and enhance product reliability. This proactive approach minimizes risks associated with packaging failures and ensures a smooth user experience.
Can I create a unique design for my glass perfume bottles, and what is the mold development process?
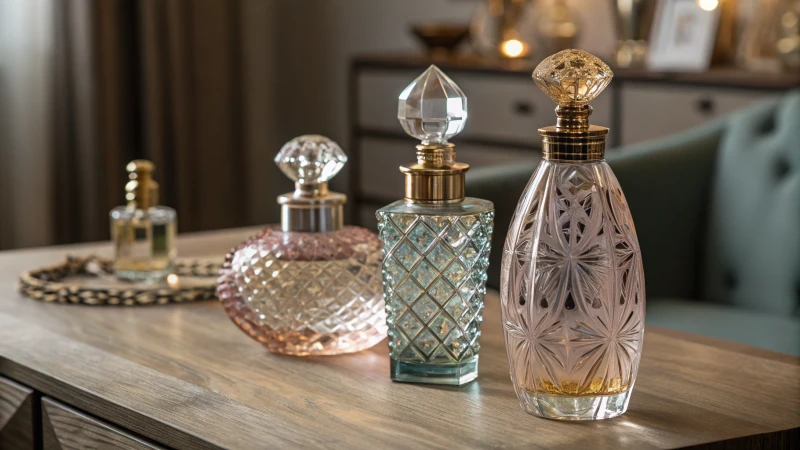
Designing unique glass perfume bottles is an exciting journey that combines creativity with technical precision. The process includes customizing designs, developing molds, and rigorous prototype testing to ensure both aesthetic appeal and manufacturability. Collaborating closely with manufacturers is essential for refining designs while meeting production requirements. This approach not only enhances brand identity but also fosters emotional connections with consumers through personalized experiences. By embracing sustainable practices in packaging design, brands can further differentiate themselves in a competitive market while appealing to eco-conscious consumers. Ultimately, the journey from concept to final product requires patience, collaboration, and innovation to create stunning bottles that resonate with customers.