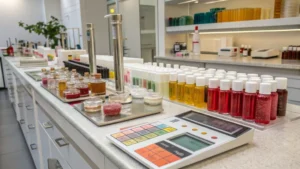
How do I test the compatibility of glass containers with different cosmetic formulations (e.g., fragrances, creams)?
Ensuring the compatibility of glass containers with cosmetic formulations is essential for maintaining product quality. This involves selecting appropriate glass types like borosilicate for sensitive products, conducting stability tests to monitor pH and color changes, and evaluating closure systems for airtightness. Chemical interaction analysis helps detect any leaching or adverse reactions that could compromise product safety. By understanding different glass types—Type I for serums, Type II for creams, and Type III for stable products—brands can prevent costly errors and enhance customer satisfaction. Regulatory compliance with standards such as ISO 10993 ensures safety while meticulous documentation aids in traceability across international markets. This comprehensive approach not only protects the integrity of cosmetics but also builds consumer trust in brand offerings.